Austrian family business relies on Bavarian
innovation
Kraus & Naimer, an Austrian company with a
long manufacturing tradition, has been
successfully supplying electrical switchgear to
industrial customers around the world for over 110
years. Franz Kraus and Lorenz Naimer founded the
company in Vienna in 1907. This was the period of
the Industrial Revolution known as the Gilded Age.
Today, the company is the global market leader in
the field of cam switches. In addition to its largest
production site in Weikersdorf (Lower Austria), the
“Made in Austria” success story continues at five
other production sites across the world (Germany,
Hungary, America, Brazil and New Zealand).
Every day, the company produces approximately
11,000 switches of various types. These are sold
through its own sales organisations in 18 different
countries across almost all continents.
Kraus & Naimer’s products are used in fields such
as mechanical engineering, shipping, rail transport
and industrial manufacturing.
The company employs some 900 people worldwide
and is known for its “innovation and quality”.
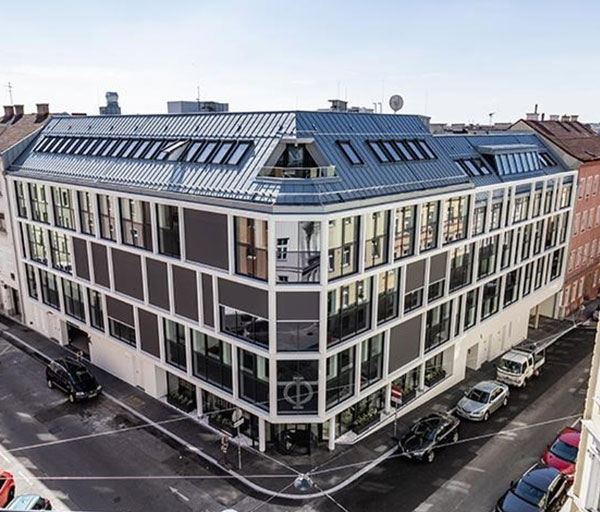
“We have always had a pioneering spirit
and the desire to pursue excellence. We
enjoy rising to the challenges of the future
and continue to concentrate our efforts on
technology, quality and know-how.”
Joachim (Ted) L. Naimer, Chief Executive Officer
The requirements
A group-wide SAP rollout saw us wanting to introduce a new document management system with the intention of replacing technologies such as SAPscript, SmartForms and other legacy systems. Besides planning to implement a uniform printer management system, the focus was also on harmonising our global corporate identity (CI) within the company’s document management system. This was to be designed and maintained at a centralised location and successively rolled out worldwide. However, it was particularly important that the solution we agreed on was able to manage the design and production of labels, as well as meet our documentation needs. The new system would also have to be capable of designing labels of different sizes within a complex business logic.
The solution
The distinguishing feature of our solution is that
the data and design levels are handled
separately. This means that business units without
software developer expertise are able to carry out
design work on the layouts of the finished
documents, or labels, themselves. It also reduces
the maintenance of our SAP programmes as they
no longer need to support technologies such as
SAPScript. Cartago was able to build on existing
expertise in the transfer of business documents
while enabling completely new design options. The
template editor for the label design now features
an improved zoom and raster functionality that
makes it easy to design and manage labels that
are sometimes only 5mm high. Image files can be
extracted from the database during the production
process, offering a quick and easy way to produce
labels and create international business
documents. Document rules controlling outputs
from the standard Cartago product have been put
in place to ensure that all templates meet the
company’s CI requirements.
At the output stage it is particularly important that
the system is able to generate the right file format
for the label printer and provide the necessary print
settings for the printer type.
Cartago partnered with SEAL Systems to provide
support with deep integration into SAP Business
Suite and high-performance spooling.
Cartago also provided a centralised monitoring
process, high-performance print outputs of labels
and document security by means of stamps and
watermarks.
Projektdaten im Überblick
- Solution rolled out at 5 of the company’s 6 worldwide production sites
- Solution rolled out to 58 printers
Kraus & Naimer im Überblick
- Operates 18 sales and service organisations
- Active in 62 countries
- Employs approx. 900 people worldwide
- Manufactures 11,000 switches of various types every day